Supplier Management Towards Sustainable Value
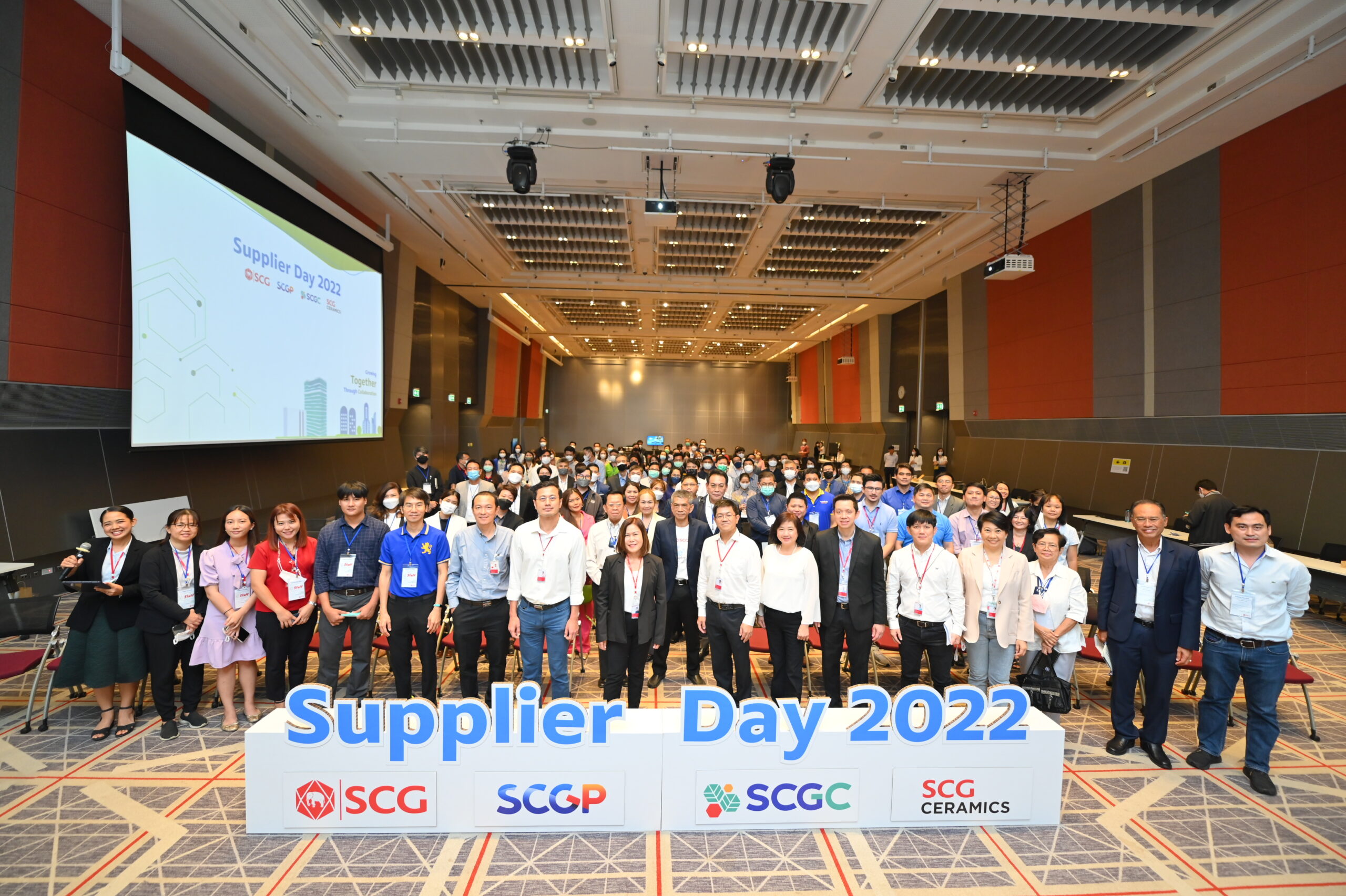
For SCG, sustainability in the supply chain from upstream to downstream is essential to its sustainable business operations. Therefore, it creates supplier management towards sustainable value. SCG intends to the selection process of suppliers with the capacity to conduct business ethically, with professionalism and preparedness to adapt to changes that impact sustainability under the risk management plan. We also value co-generation of opportunity with our suppliers, under an efficient assessment program.
Target
- 95% of the procurement spend comes from suppliers who commit to comply with Supplier Code of Conduct by 2023.
- 100% of supplier in procurement spend over million baht processed through the annual Environmental, Social, and Governance (ESG) assessment
- 100% of operation contractors certified under SCG Contractor Safety Certification every year from 2012 onwards.
Strategy
1. Select and assess suppliers with the capability for sustainable business
Select suppliers on the basis of commitment to comply with SCG Supplier Code of Conduct, and capacity for sustainable business. Conduct for assessment and certification of suppliers annually and continuously in order to mitigate risk in the supply chain.
2. Assess risks and classify suppliers into groups
Conduct spend analysis and business risk assessment, taking into account Environmental, Social and Governance (ESG) factors. Prioritize risks that may affect SCG business. The results are then used to classify suppliers and frame a strategy and supplier development plan corresponding with the risk.
3. Develop supplier’s capability towards sustainability
Organize and plan a development program aligned with the risk, while seeking to strengthen the supplier’s competitiveness to facilitate their grow alongside SCG.
4. Raise awareness, knowledge and people’s competency
Establish a Procurement Sub Academy Steering Committee to enhance the knowledge and competency of employees. Share knowledge, information, operational guidelines with procurement entities in both public and private sectors with an emphasis on procurement and sustainability. This is to ensure that our people work effectively in line with targets.
Management
1. Annually and continually, conduct risk assessment and certification of every single supplier, on the basis of enterprise risk management framework and act according to “SCG Sustainable Procurement Framework” that addresses ESG aspects alongside spend analysis.
2.Segmentation of supplier into four groups: tier 1 supplier, Significant Supplier-Critical Supplier, Significant Supplier-High Potential Sustainability (ESG) Risk Supplier and Critical Non-Tier 1 Supplier.
3.Formulate plans to enhance supplier’s capacity in sustainable business effectively addressing ESG issues, continually and effectively.
4.Foster business collaboration in accordance with ESG by regularly communicating with supplier through activities such as workshop, seminar.
5. Establish a committee to advance knowledge and competency of staff in the professions of procurement, supply and logistics, as well as organize sharing of knowledge and practice with public and private sector procurement bodies.
Governance Structure: Oversight and Implementation of the supplier ESG program
Governance Structure: From the Board of Directors to the Sustainable Supplier Committee
SCG has adopted supply chain management as a key strategy for risk reduction and organizational resilience by establishing responsible units at both the corporate and business levels. These units work to enhance the efficiency of all processes across the value chain while maximizing benefits for stakeholders.
The SCG Board of Directors provides oversight of supply chain management policies, strategies, and the supplier ESG program. This oversight extends beyond addressing current supply chain challenges to ensuring a long-term, comprehensive strategy for sustainable operations.
To execute these responsibilities effectively, the Board delegates oversight authority to the Sustainable Development Committee SCG (SDC), chaired by the President and CEO, who is also a member of the SCG Board of Directors. The SDC is responsible for supervising and driving sustainability efforts across SCG, ensuring alignment with corporate strategies and ESG commitments.
The Sustainable Development Committee (SDC) consists of five subcommittees that oversee various sustainability dimensions, including economic, environmental, and social aspects. One of these subcommittees is the Sustainable Supplier Committee, which plays a crucial role in implementing and strengthening the supplier ESG program under the broader governance of the Governance & Economic Excellence Committee.
Role of the Sustainable Supplier Committee
The Sustainable Supplier Committee serves as the central mechanism for integrating ESG principles into SCG’s supply chain management. Its key responsibilities include:
• Establishing supplier screening and risk assessment criteria to ensure due diligence and responsible sourcing practices
• Prioritizing suppliers based on risk levels to mitigate potential ESG-related risks across the supply chain
• Creating sustainable value by enhancing supplier capabilities through collaborative programs and support initiatives
• Providing training and development programs for SCG buyers, ensuring they uphold supplier ESG program requirements.
The Sustainable Supplier Committee reports on supplier management progress to the SDC, ensuring that all actions are aligned with the Board of Directors’ strategy, ESG principles, and SCG’s Supplier Code of Conduct.
Additionally, the committee continuously improves procurement practices by refining the Sustainable Procurement Framework and enhancing the SCG Supplier Portal to promote efficiency, transparency, and accountability in sustainable supply chain management. This approach reinforces SCG’s commitment to responsible sourcing and long-term supplier engagement.
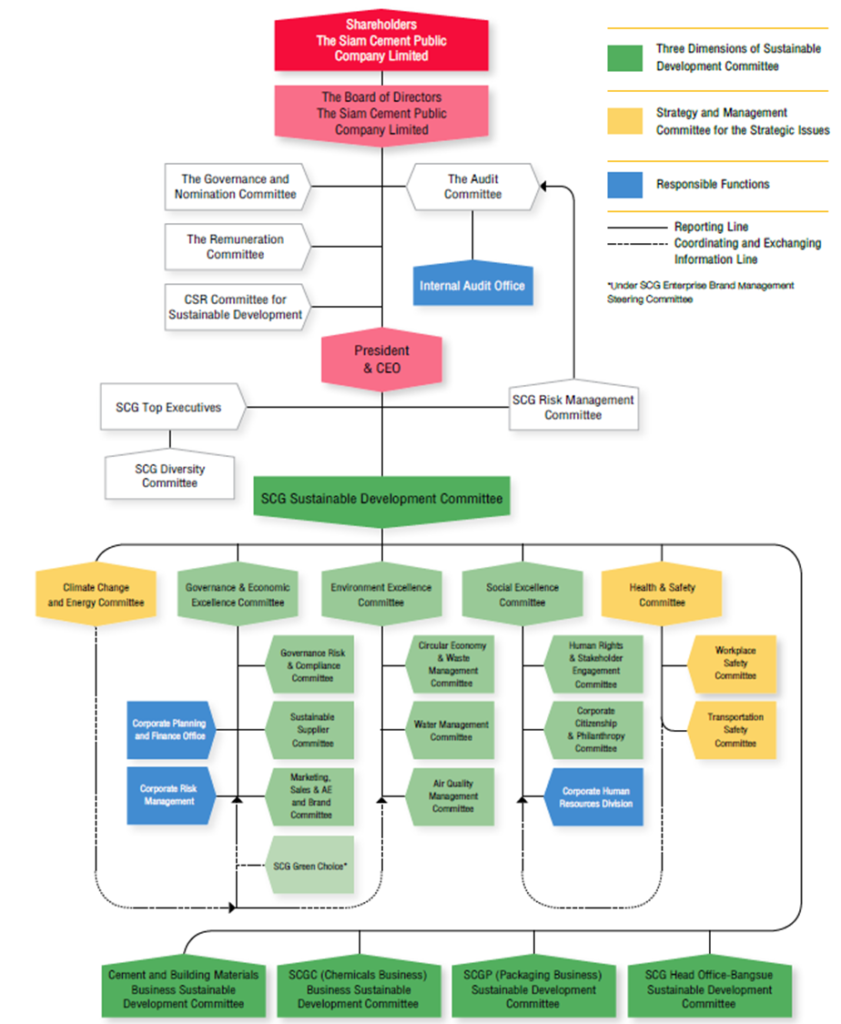
SCG Supplier Portal
SCG Supplier Portal is the procurement practices tool and communication platform for managing and routinely communicating with SCG suppliers. This is to manage suppliers for ESG risk screening and assessment in accordance with the Supplier Code of Conduct and a proactive approach for managing raw materials for business continuity, costs, quality, and delivery times. The SCG Supplier portal includes the following features:
1. Supplier Code of Conduct signing to express commitment to comply with SCG Supplier Code of Conduct
2.Collecting supplier sustainability information, submitting documents, communicating ESG screening and assessment criteria and tracking ESG performance program
3.Verifing supplier information, managing documentation, and screening supplier who meets SCG ESG criteria.
4.Risk management through risk assessment, risk mitigation, and collective action plan including monitoring financial stability, conducting background checks, and managing compliance with regulatory and ESG requirements.
5.Building and maintaining positive relationships with supplier through communication, collaboration, and feedback as well as whistleblowing channel.
Company Buyers Training Program
To provide the knowledge and abilities to understand th target of ESG program and procurement practices, Sustainable Supplier Committee conducts the E-learning system in order to enhance the skills and abilities of company buyers.
The E-learning system was established to support learning and understanding of the Sustainable Procurement Framework, which is a guideline for SCG Group companies to implement sustainability with their suppliers. The document establishes a process for risk management encompassing economic, environmental, social, and governance (ESG) as well as approach that is appropriate to the risk level, taking into account quality, quantity, delivery of products and services according to the customer’s requirement, and compliance with laws and quality assurance systems, with a view to preventing and mitigating risk. The online learning takes about 30 minutes and there is a Post Test system to measure knowledge after studying.
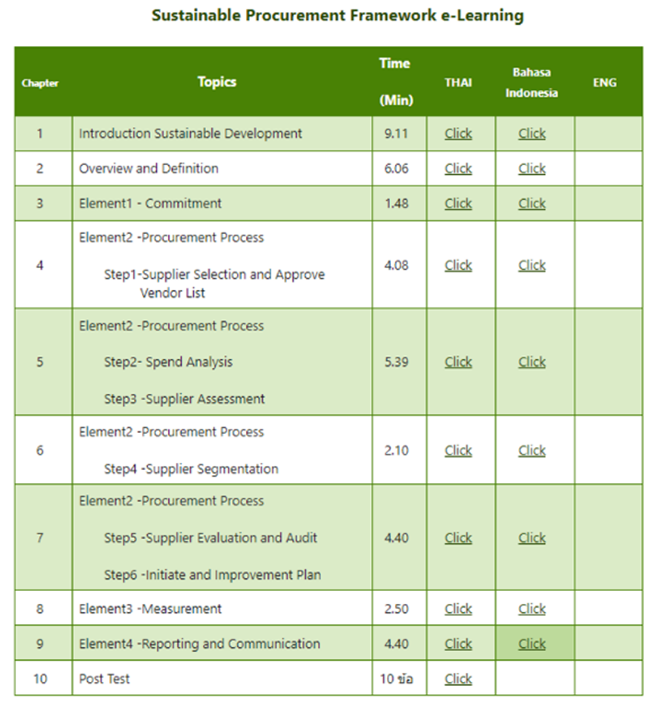
Supplier Code of Conduct
SCG conducts its business with integrity in line with the principles of good corporate governance and SCG Code of Conduct and is committed to nurturing and supporting society and the environment in accordance with the sustainable development approach to achieve an economic, social, and environmental balance, enabling them to grow alongside each other in a sustainable way. To disseminate this concept to its suppliers, who play a vital role in SCG’s business success, SCG has established this Supplier Code of Conduct to provide guidance for applying relevant principles and concepts to their businesses and encourage them to adopt them as policies, standards, and guidelines for conducting business with their own suppliers in order to achieve fairness and transparency and generate value for stakeholders across the value chain sustainably, from the process of designing, procurement, manufacturing, provision of services, distribution and logistics, all the way to waste and post-consumer material management, as well as to promote among its suppliers good citizenship and corporate governance for society and the environment.
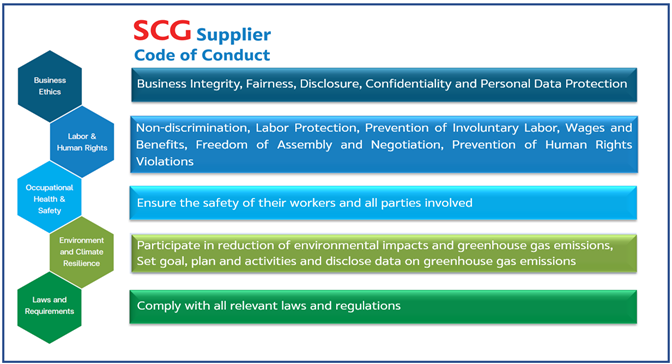
SCG Sustainable Procurement Framework
SCG prioritizes supply chain management, by considering and managing risk across the entire supply chain- starting from the process of sourcing of raw materials, material and equipment used in production, transport, trading, delivery of products and services in order to respond to the customer’s needs and to prevent any impact upon the trust of customer and stakeholder.
The Sustainable Procurement Framework has been established and applied by all companies under SCG operation. It consists of 4 components which are
- Commitment to ensure that SCG conducts business with suppliers systematically, fairly, transparently, at the same time enabling suppliers to operate with SCG Supplier Code of Conduct.
- Procurement Practice towards Supply Chain ESG Risk management Process to identify, assess and manage risks in order to ensure that suppliers comply with guidelines under relevant regulations and laws, ethical issues, human rights, occupational health and safety, environment, and other laws and regulations.
- Measurement to measure supplier performance and procurement efficiency according to the Sustainable Procurement Framework
- Reporting and Communication to ensure that sustainability implementation of the supplier, as well as efficient procurement proceedings, performance must be reported and communicated to stakeholders at multiple levels.
The Sustainable Procurement Framework has been established and applied by all companies under SCG operation, complied with Significant Supplier, which includes both Critical Supplier and High Potential Sustainability (ESG) Risk Supplier, General Supplier, Focused or High Opportunity Supplier, and *Critical Non-tier1 Supplier shall adapt the Sustainable Procurement Framework in place in their own supply chain management to ensure supply chain security and risk mitigation.
*Critical Non-tier 1 Supplier means suppliers who do not directly produce and distribute goods and services to SCG. However, they deal with products and services that are important to , Significant Supplier-Critical Supplier of SCG.
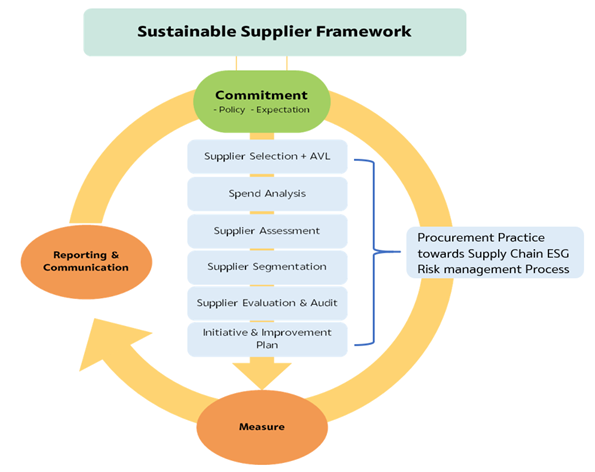
Procurement Practice towards Supply Chain ESG Risk management Process
Step 1 Supplier Selection, Approved Vendor List
Compilation of an Approved Vendor List requires that Suppliers adhere to and comply with a set of Minimum Requirements. The substance and boundary of the guideline are formulated by rules, regulations and laws governing ethical business conduct, human rights and labor rights, occupational health and safety, environment, along with any other relevant legal and regulatory provisions.
Minimum requirement
- Be a Signatory to SCG Supplier Code of Conduct, or Signing an Expression of Commitment to comply with SCG Supplier Code of Conduct. In the latter case, it is required that the supplier has an existing written code of conduct or business approach that is compatible with SCG’s.
- Supplier operating on site must acknowledge and comply with Life Saving Rules
- Supplier to production process must be certified by SCG Subcontractor Safety Certification System: SCS
Step 2 Spend Analysis
Conducting Spend Analysis, the result of which is to be used as a tool in risk assessment and risk management of supplier. The scope of Spend Analysis covers all types of procurement and sourcing, accounting for the following Spend Amount categories and Supplier Location.
Step 3 Supplier assessment for Screening
Conducting Supplier Assessment by considering the impact of supplier upon risk in procurement and business conduct in order to identify Significant Supplier-Critical Supplier and ESG Assessment in order to identify *Significant Supplier, which includes both Critical Supplier and High Potential Sustainability (ESG) Risk Supplier. The Supplier Assessment process should be carried out at least once a year, consistently at year-end encompassing Risk Assessment related to the supplier’s economic aspects and their sustainability or ESG performance covering Environment, Social, and Governance factors.
- Significant Supplier- Critical Supplier means Suppliers, and Distributors of products and services that are significant to SCG’s business operations, such as high purchasing volume, critical components of the product, non-substitutable products. Critical Supplier is considered on the basis of:
- High Volume. (High Volume purchase classification is defined by individual business unit/company) and/or
- Critical Component. The supplier sells products/services that are critical to the production processes or business and/or
- Business relevant and/or
- Non-Substitutable/ Oligopoly/ OEM
- Non-Substitutable: Any suppliers that sell products/services that cannot be sourced elsewhere/other suppliers cannot substitute
- Oligopoly : suppliers deal in products/services where there are very few players
- OEM (Original Equipment Manufacturer
Critical Non-tier 1 Supplier means Suppliers who do not directly produce and distribute goods and services to SCG.
- Significant Supplier – High Potential Sustainability (ESG) Risk Supplier means suppliers producing and delivering products and services with high likelihood to cause negative social impact (e.g. in human rights issues, caring for employees and workers); environment (such as waste management) and governance (e.g. compliance with the law). Risks that take into account sustainability issues related to those suppliers with high risk to cause negative impact on ESG criteria following:1. Environmental Risk. For instance, on water management, waste, energy, chemicals, air pollution, Green House Gas emission, efficient resource use
- Social Risk. These include labor practice (use of child labor, forced labor), human rights, health, safety, complaints, non-compliance with relevant laws and regulation.
- Business/Governance Risk. Legal compliance, corporate image, and compliance with permit/license and other related factors following.
- Country-specific risk is a risk that arises from the uncertainty of economic, social, and political conditions, or other external factors such as natural disasters that occur in the area where the supplier is located.
- Sector-specific risk is a risk that arises from a sector’s distinct characteristics regarding labor situation, energy consumption, resource intensity, emissions, or pollution potential (e.g. manufacturing, service provision, agriculture).
- Commodity-specific risk are risks that arise from the characteristics of the industry where the business partner operates and the products that the supplier produces or sells.
Should any supplier fail to comply with ESG requirements and SCG Supplier Code of Conduct, SCG reserves the right to temporarily suspend procurement or excluded them from the contracting or remove them from the approved supplier list.
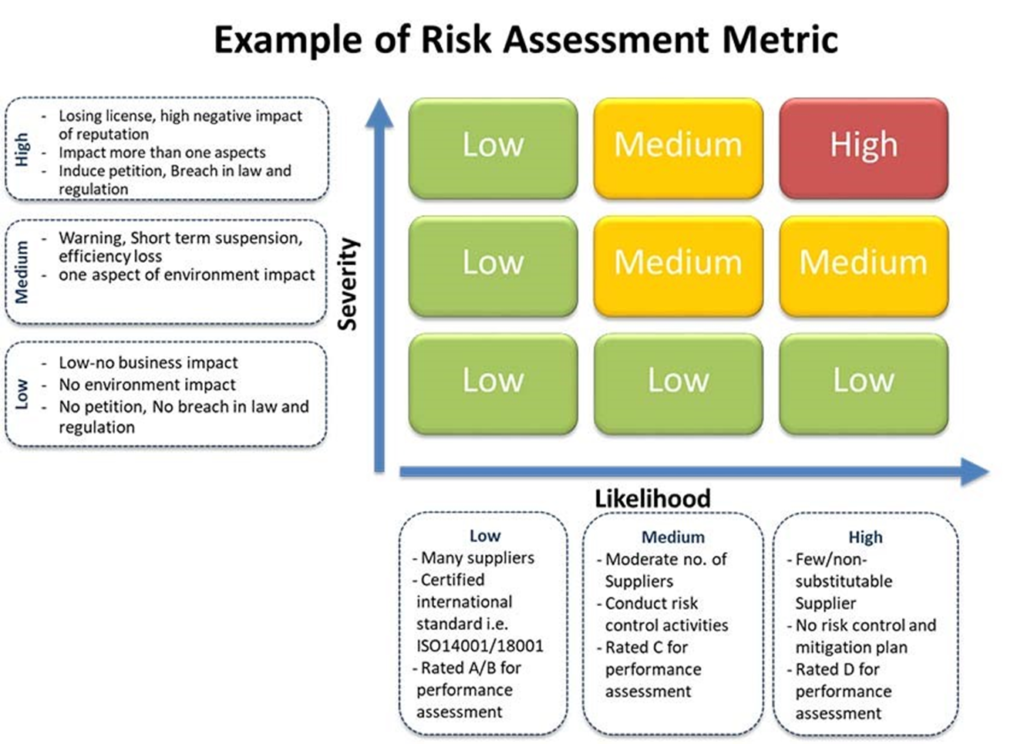
Step 4 Supplier Segmentation
Managing supplier according to the level of impact and risk, based on results of Spend Analysis and Supplier Assessment. Prepare a Comprehensive Assessment plan or Audit Plan, as well as plan for monitoring and corrective action.
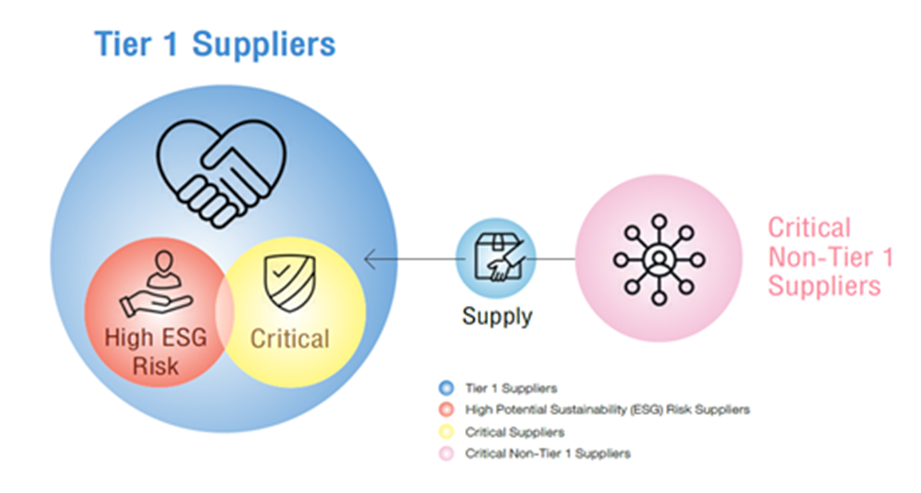
• Significant Supplier–Critical Supplier /Business relevant Perform audit and plan risk management
• Significant Supplier–High Potential Sustainability (ESG) Risk Supplier. Conduct Supplier Assessment, along with planning of long-term collaboration to enhance the suppliers’ capability.
• General Supplier. Supplier is a signatory to SCG Supplier Code of Conduct. Or the supplier has an existing business code of conduct/regulations/business guideline that is compatible with SCG Supplier Code of Conduct.
• Supplier with high potential or significant business opportunities (Focused or High Opportunity Supplier) should consider opportunities for collaboration to develop products or services. This includes jointly planning with business partners to drive development and advance business growth together.
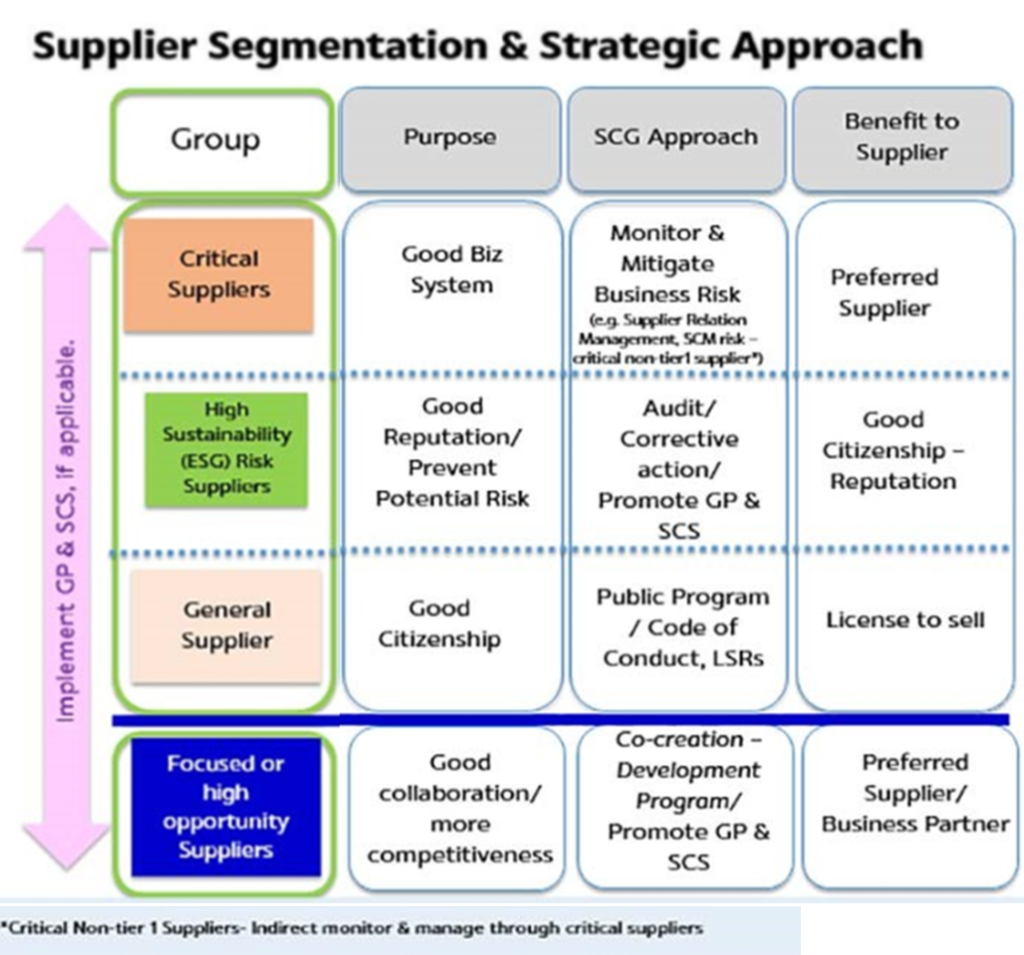
Step 5 Supplier Evaluation and Audit
SCG has a process for regularly Supplier desk assessments and Supplier on-site assessments and evaluating suppliers’ performance at least once every 3 years, or 100% coverage within 3 years in terms of delivery scheduling covering product and service quality, as well as criteria for assessing environmental, social and governance (ESG) risks in their operation which considers the impacts on environment, society along with business continuity comply with law, regulation, and international standard such as ISO9001, ISO14001, ISO45001, ISO50001, TIS/OHSAS18001, UDHR, UNGC, UNGP, and ILO etc.
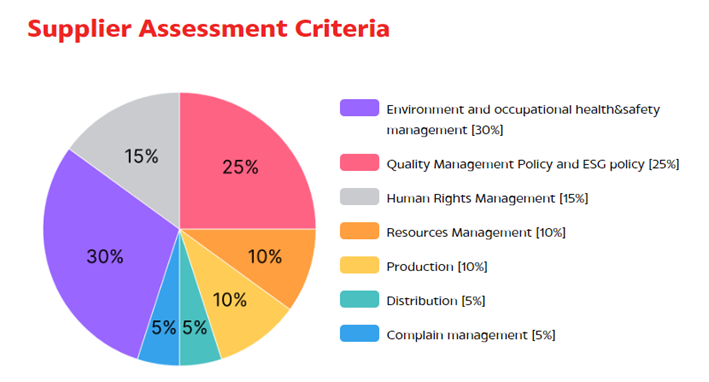
Minimum weight of ESG for assessment process*
Suppliers shall meet a minimum requirement 70%
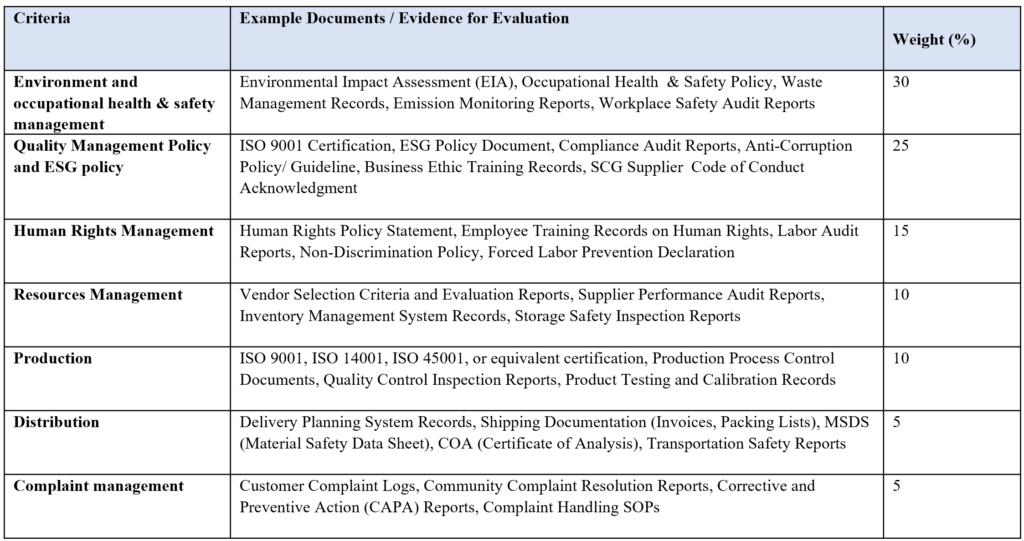
Approach
- Evaluate supplier’s capability by taking into account Environmental, Social and Governance (ESG) impact.
- Use Site Visit Questionnaire/Supplier Desk Assessments/Third-Party Audit (Independent Accredited Auditing Company) to inquire into business practice as well as ESG impact.
- Conduct On-Site Visit/Supplier Desk Assessments/Third-Party Audit (Independent Accredited Auditing Company) , and inform results of assessment along with supplier development plan, to increase the capacity of sustainable enterprise management.
Significant Supplier-Critical Supplier
Conduct Supplier Assessment, according to the type of business risks efficiently, including the following:
- Plant Reliability Assessment, through site visit and review of business operation/approach
- Supplier Desk Assessments
- On-site Audit to be conducted by an internal entity within the BU/company
- Monitor critical non-tier 1 supplier, using Significant Supplier-Critical Supplier Questionnaire or through interviewing, or conducting media and stakeholder analysis
- Third-Party Audit (Independent Accredited Auditing Company), or business assessment criteria, as well as Environmental, Social and Governance impact.
Significant Supplier-High Potential Sustainability (ESG) Risk Supplier
Perform Supplier on-site assessments through either a Third-Party Audit (Independent Accredited Auditing Company) or by an internal entity within the Business Unit.The ESG assessment encompasses specific criteria, accompanied by actionable recommendations aimed at addressing any identified gaps. In terms of audits, there are Supplier Desk Assessments, On-Site Audit, and Third-Party Audit(Independent Accredited Auditing Company) . If a supplier is unable to meet the specified standards and criteria, the company will consider temporarily suspending the purchase or removing the supplier from the list of vendors. By conducting an ESG assessment, if they are identified as a Significant Supplier-critical supplier with a high risk rating, SCG will conduct thorough investigations and develop timely corrective and preventive actions, ensuring continuous follow-up and re-assessment until improvements are achieved.
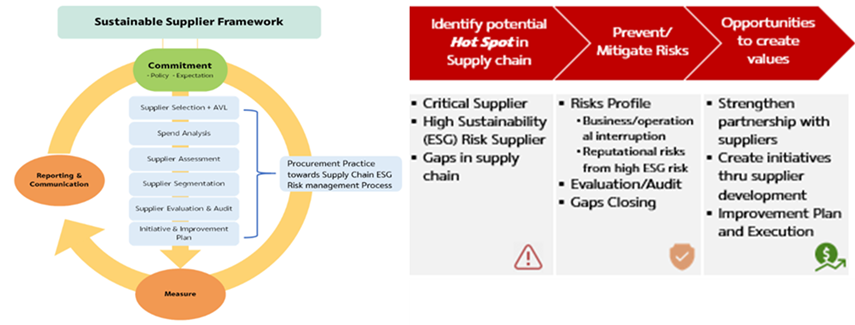
Step 6 Initiative and Development Plan
SCG aims to engage with suppliers, communicating its expectations and intentions regarding sustainability management, while exploring opportunities to enhance capability, competitiveness, and synergy within the supply chain. To achieve this, SCG will establish work plans, projects, and activities that support suppliers’ sustainable business practices in alignment with the company’s goals. Additionally, SCG seeks to strengthen and expand stakeholder participation in the supply chain through initiatives like green procurement, carbon-label certification, consultancy, advisory assistance, and incentives for suppliers’ efforts in environmental and social management systems.
Following an Audit, consider the risk and findings identified by the Audit to form basis for a suitable action plan. The framework for consideration covers the following 3 scenarios:
- If the risk is business risk to SCG, there has to be a work plan to manage such a risk.
- If the risk is business risk to the supplier, recommendation for improvement must be given. Particularly for Significant Supplier-High Potential Sustainability (ESG) Risk Supplier, the recommendation is intended for formulation of a Corrective Action Plan to improve environmental, social and governance gaps. The resultant Corrective Action Plan, or Preventive Plan has to be monitored and reported on quarterly basis, within 1 month after end of quarter.
- In case of a potential opportunity to develop products and services, or business opportunity, a Co-creation plan with the supplier should be considered.
Sustainable Supply Chain Measurement
To ensure implementation of sustainability by supplier, and efficient proceeding of procurement as well as compliance and compatibility with the Sustainable Development Framework under governance principle, performance has to be measured by taking into account the following:
Examples of Measurement
Implementation | Key Performance Indicators |
Supplier Selection, Approved Vendor List | 1.Number of signatures committing to compliance with SCG Supplier Code of Conduct 2.Number/percentage of new suppliers having done Supplier Desk Assessments regarding ESG compliance. |
Spend Analysis | 1.Percentage of procurement value from suppliers who have shown commitment to compliance with SCG Supplier Code of Conduct. 2.Spend Analysis Result Report |
Supplier Assessment | 1.Percentage of suppliers that have passed Sustainability Risk Assessment 2.Minimum weight of ESG for assessment process* 3.Result of Supplier Assessment |
Supplier Segmentation | 1.Result of Supplier Segmentation |
Supplier Evaluation and Audit | 1.Percentage of evaluation and audit of Significant Supplier-Critical Supplier/Significant Supplier-High Potential Sustainability (ESG) Risk Supplier 2.Number of Corrective Action Request-CAR 3.Supplier Evaluation and Audit result |
Initiation and Improvement Plan | 1.Percentage of implementation of a risk management plan or corrective action plan. 2.Number of work plan/project/activity to advance sustainable business practice of the supplier 3.Number of project or added value to business resulting from collaboration with suppliers 4.Percentage of suppliers undergoing safety training |
Significant Supplier Monitoring
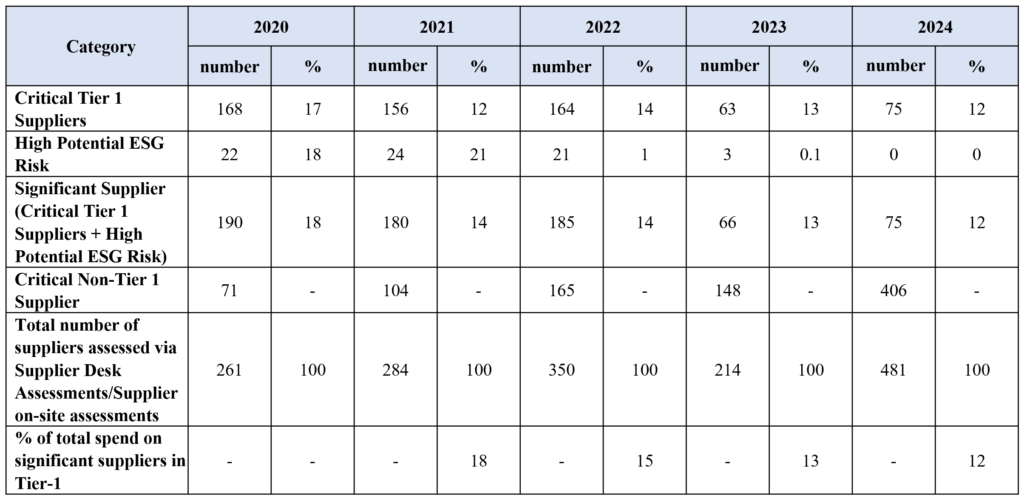
Supplier with Corrective Action Plan
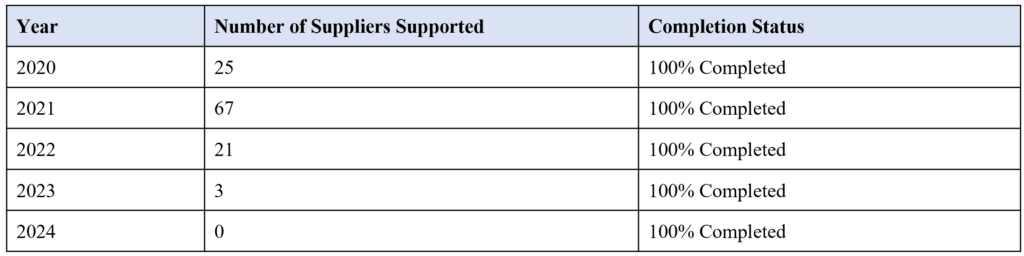
Supplier Development and Capacity Building Program
To further strengthen supplier capabilities, SCG has implemented a comprehensive training program designed to enhance their capacity in ethical principles, legal and regulatory compliance, technical knowledge, and the integration of Environmental, Social, and Governance (ESG) into their business operations. This initiative aims to drive sustainability throughout the value chain while aligning with SCG’s Sustainability Goals, ensuring that suppliers can meet national and international standards while adapting to sustainability challenges.
SCG fosters strong collaborations and continuous improvement across all suppliers, with a strategic focus on three key groups.
1. Focused or High Opportunity Supplier: collaborates with suppliers that have the potential to co-develop products through co-creation plans, SCG strengthens partnerships, fosters innovation, and drives mutual growth, ensuring long-term value creation within the supply chain.
2. Significant Supplier – Critical Supplier: ensures long-term collaboration and supply chain stability by
1) strengthening supplier relationships to enhance efficiency and reliability
2) promoting business continuity by securing essential materials and services and
3) supporting suppliers in adopting best practices for quality and operational excellence.
3. Significant Supplier – High Potential Sustainability (ESG) Risk Supplier: actively supports suppliers in this category by promoting sustainable business practices and mitigating environmental and social risks. The company works alongside suppliers to elevate their ESG performance through: Environment risk such as Efficient resource use, waste management, GHG emissions reduction. Social risk such as ethical labor practices, workplace safety, human rights. Governance risk such as legal compliance, corporate integrity, and adherence to regulatory requirements.
Supplier Capacity Building and Development Program 2024
GHG Scope 3 Supply Chain Decarbonization
Since 2022, SCG has continuously enhanced supplier capabilities through its Supplier Decarbonization Program to reduce Scope 3 GHG emissions. The initiative began with Supplier Day (2022), followed by the first Supplier Workshop (2023), where 12 partners were trained on GHG emissions calculations. In 2024, SCG expanded its efforts by collecting emissions data from 113 suppliers in the categories of Purchased Goods and Services and Fuel- and Energy-Related Activities (not included in Scope 1and Scope 2) , which were used extensively in production and thus had a significant impact on Scope 3 emissions, divided into 20 strategic suppliers (already tracking emissions) and 93 high-impact suppliers (not yet collecting data). Additionally, in-depth workshops were conducted for 19 high-impact suppliers to improve GHG data management. This ongoing effort reflects SCG’s commitment to building supplier readiness for carbon emission policy and regulation, and sustainable business practices, ensuring long-term growth and a low-carbon value chain.
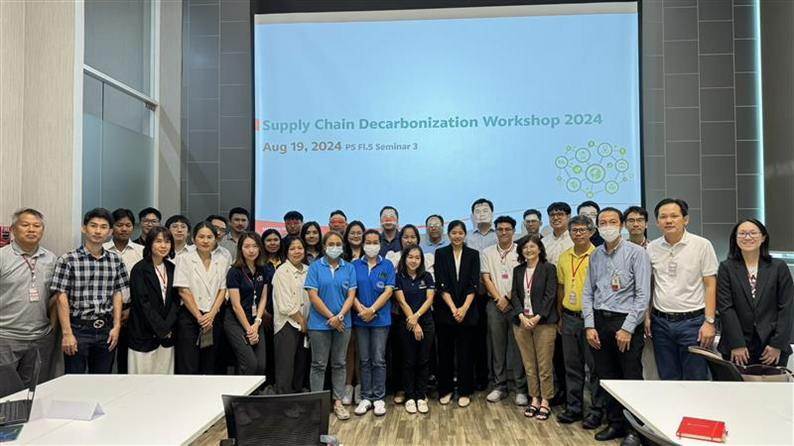
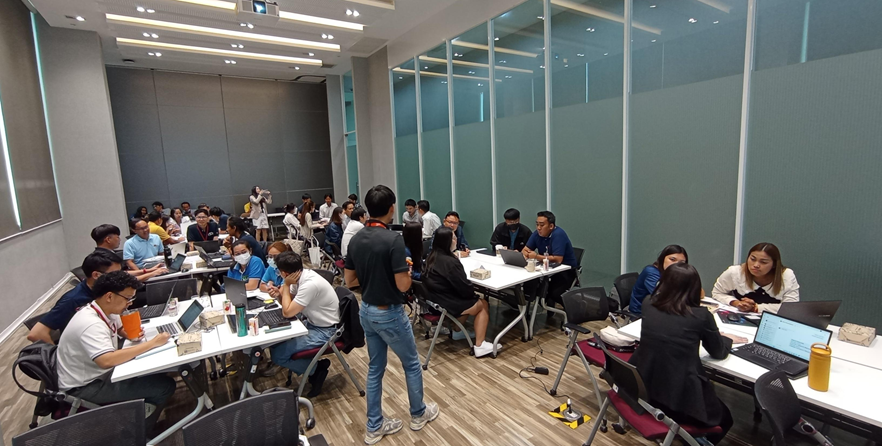
SCGC Safety Practice Day 2024
“Moving Forward” – Advancing with Care toward Sustainable Safety
SCGC recognizes the importance of elevating safety standards in collaboration with SCGC’s suppliers to promote efficient and safe operations. The focus lies on establishing practical safety standards that can be effectively implemented, providing knowledge and sharing insights on safety to enhance work efficiency, listening to feedback from suppliers to find collaborative solutions, and honoring outstanding safety performances.
To achieve these goals, SCGC organized the SCGC Safety Practice Day 2024, a platform not only for promoting workplace safety but also for fostering an open dialogue between SCGC and suppliers. The event aimed to exchange ideas and collaboratively develop sustainable safety standards, ultimately enhancing operational efficiency and safety across all sectors.
The event took place on July 31, 2024 with participation from 80 suppliers, totaling 143 attendees from;
1. Suppliers with significant working hours at SCGC sites during 2023–2024.
2. Suppliers with a strong safety record.
3. Suppliers who have provided feedback or suggestions on safety practices.
Awards Presented The Best Safety Performance Award – 10 awards, Outstanding Engagement Award – 7 awards, Exemplary Safety Culture Award – 1 award, The Best Safety Improvement Award – 5 awards, The Best Operation and Performance on SCGC System – 5 awards
The SCGC Safety Practice Day 2024 received highly positive feedback from participants. According to the survey, 97% of attendees expressed satisfaction with the event and the knowledge gained.
This initiative not only fostered a deeper understanding of SCGC’s safety standards and management systems but also strengthened confidence in SCGC’s collaborative approach with suppliers. The event successfully enhanced partnerships and laid the groundwork for continuous improvements in sustainable safety practices.
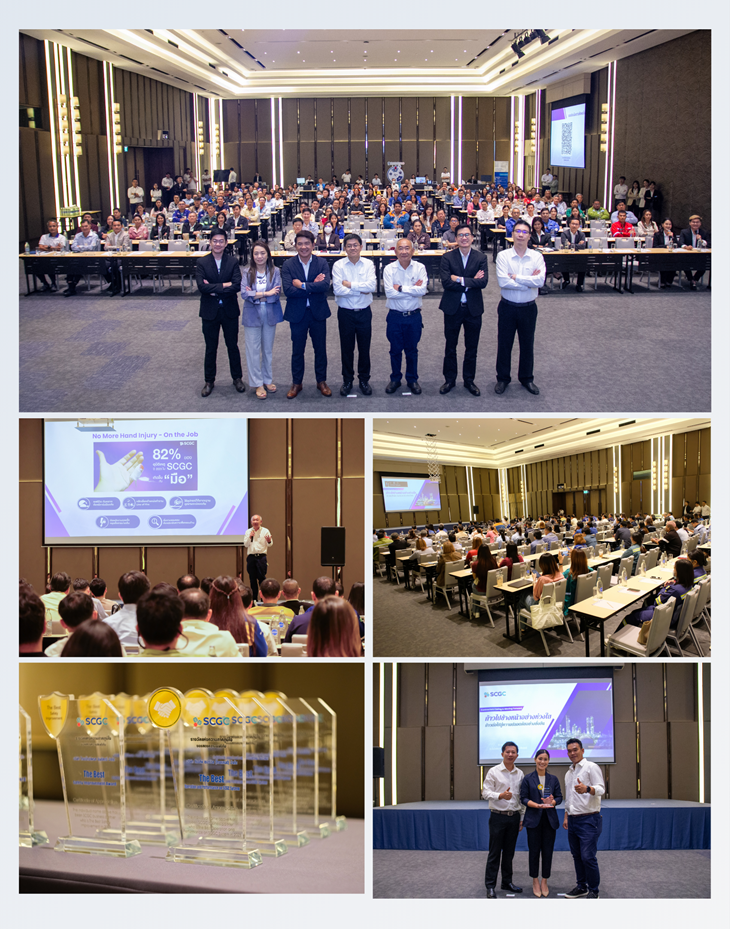
SCG Smart Living – Housing Product Solution Business: Advancing the Circular Economy
SCG Smart Living actively promotes and drives the Circular Economy policy through sustainable material management. Currently, Aluminum Pallets have an average lifespan of approximately two years before being sold as scrap, a process that involves fluctuating market prices and additional time for disposal.
This project mitigates raw material cost risks associated with new Aluminum Pallet production, which is impacted by global aluminum market price volatility. Under this initiative, business partners buy back expired pallets at a pre-agreed price, ensuring stability while facilitating the rycling process. The collected aluminum is then melted and repurposed as raw material for new production. This approach benefits both SCG and its suppliers by improving cost management and operational efficiency, while reinforcing the Circular Economy principle by optimizing expired material handling and enhancing procurement stability.
In 2024, three business partners joined the project, generating an estimated value release of 10% compared to traditional scrap sales, amounting to approximately THB 4 million. Additionally, the initiative significantly improved efficiency, reducing procurement process time by 500 hours per year, equivalent to THB 0.5 million in cost savings.Through this innovative approach, SCG is enhancing resource circularity, cost efficiency, and procurement resilience, setting a benchmark for sustainable business practices.
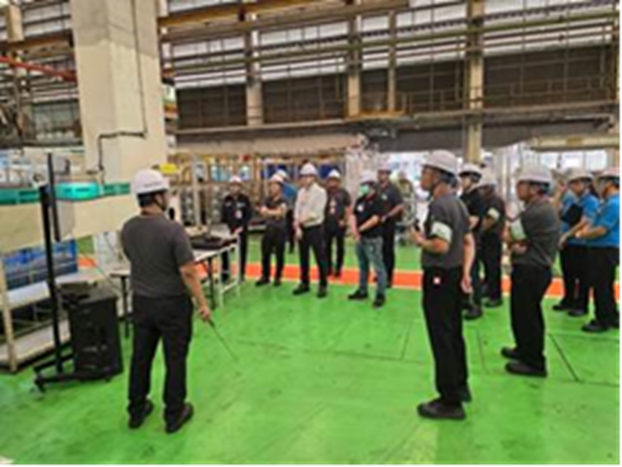
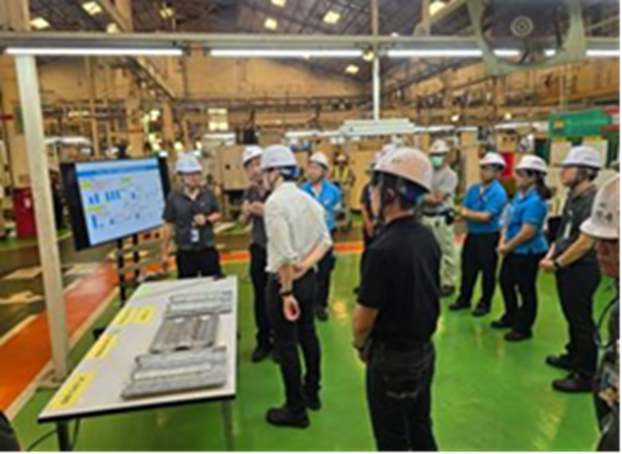
In-depth Technical Support Program
Our In-depth technical support programs and technical knowledge support aim to systematically build ESG performance in key ESG areas .The programs include training, baseline assessments, collaborative system development, and regularly tracking progress.
- Climate Change Supplier Engagement Workshop
SCG organized a Climate Change Supplier Engagement Workshop in July 2022 with the objective of creating knowledge and understanding of climate change issues in the supply chain by providing the information and resources they need to reduce greenhouse gas (GHG) emissions, building relationships with suppliers and working together to find solutions that work for both parties, and encouraging suppliers to act on climate change. The participant group consists of 12 suppliers with medium-to-large purchasing volumes that are willing to act on climate change and have the greatest potential to reduce emissions.
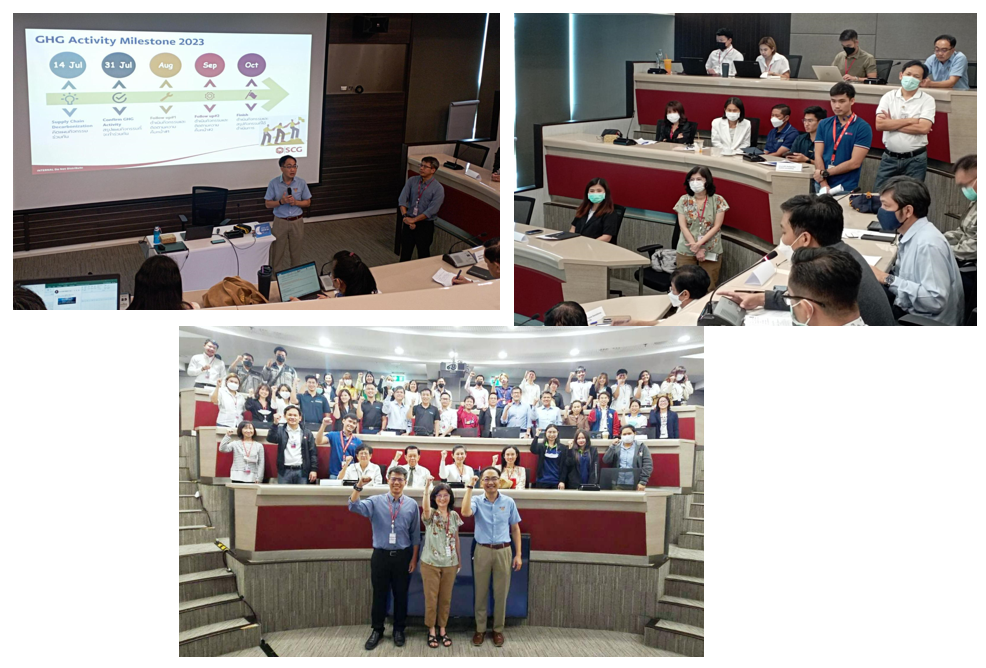
2. Towards Net Zero: Developing Supplier’s Capacity to Provide EV Services:
Limestone Trucking EV
Cement and Building Materials Business collaborates with suppliers to pilot the first fleet of six EV Mining Trucks in Thailand for delivery of limestone, the main material for cement production. It achieves GHG emissions reduction by 108 ton CO2eq per vehicle per year, equivalent to planting 11,333 trees per year. Working with supplier, SCG studied EV usage to plan and analyze numbers and optimal positioning of charging stations. The target is set to replace all conventional with EV fleet in the operation of
Siam Cement (Thung Song) Co.,Ltd. by 2025, and subsequently scaling up to other cement factories.
This project promotes and aligns with the Green Mining of the Industry Ministry and Department of Primary Industries and Mines.
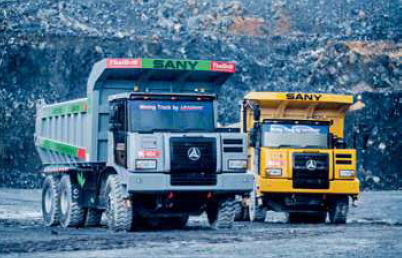
EV Forklift
SCG trialed EV Forklift in 2021. At present, it has been able to replace 400 conventional forklifts with
electric ones. Ceramic factory under Cement and Building Materials Business piloted EV forklifts to test performance in different functions alongside collection of emissions data for the next phase of development. The target is to replace an existing fleet of 30 conventional forklifts whose contract
expires in 2023 with EV forklifts and identify potential suppliers for providing EV forklift service that meets
requirements of factories.
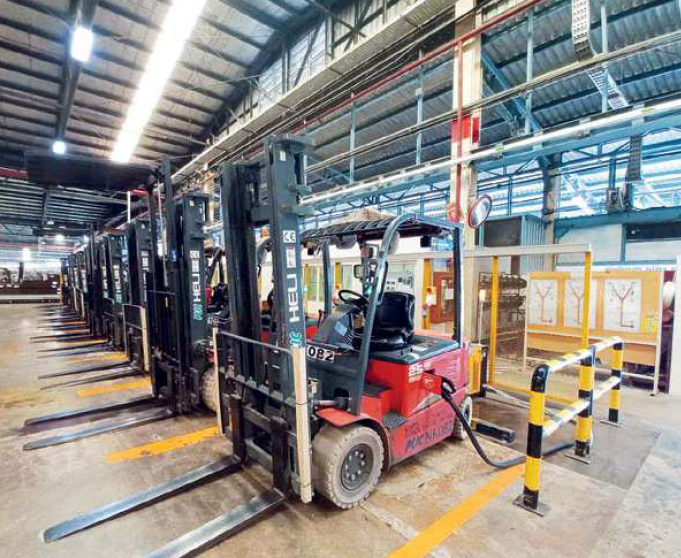
3. Towards Net Zero: Tackling Supply Chain Emissions
SCG is working with supplier to reduce GHG Scope 3 emissions. This starts with SCGC (Chemicals Business) partnering with suppliers who are traders in chemicals and packaging accounting for over 80% of procurement value (128 suppliers) to collect emissions data as baseline for project development.
4. Go Green: Increasing Green Supplier
SCG has selected potential suppliers for the environment development, supporting them to be
certified by ISO 50001, ISO14001, the Industry Ministry’s Green Industry Standard, and listing in SCG’s Green Procurement registry. This is done through auditing, provision of advisory service and support until the supplier meets the criteria and benchmarks. For example, in 2022, SCGC (Chemicals Business) worked with 8 suppliers developing 7 items (6 products and 1 service) to the SCG Green Procurement list,
boosting green procurement share in SCGC’s total procurement value from 14% to 17%. The next step is to develop a re-assessment performance process to ensure that the company maintains the green procurement practices.
Collaboration Network
SCG collaborates with eight leading companies in Thailand to jointly establish the Thailand Supply Chain Network (TSCN), which aims to help Thai businesses expand to overseas markets throughout the entire supply chain while adhering to sustainable business practices and exchanging information, knowledge, experiences along with enhancing awareness and understanding about ESG with industry peers.
In March 2023, TSCN organized a training session to address environmental issues called “The Power of One: Taking Action to Reduce GHG Emissions,” Batch 1 for greenhouse gas accounting Scope 1 and Scope 2, in which SCG has co-designed the curriculum and will be co-leading this training course.
DOCUMENT DOWNLOAD
SCG Supplier Code of Conduct
SCG Procurement and Vendor Selection Policies and Guidelines
SCG Human Rights Expectation Letter
SCG Guidelines for Green Procurement